Automated Cap Lamp Output Tester
Automatic Light Beam Testing System
Highlights
- Tests and logs light output in less than 10 seconds
- Easy to use
- Provides results in a Table format
- Customizable solution
- Adaptable software
- Components
- Custom-built 1.2m-long light box
- Light meter
- RFID tag reader
- Laptop/tablet running custom software (laptop/tablet supplied by the customer)
- Components
Features
Wi-Fi or RFID tracking tag enabled
Tags are primarily used for location tracking of personnel and access control. A key benefit is pinpointing the location of miners during an emergency.
Tag is powered by the lamp
Once installed into the NLT lamp, there is never a need to change the tag battery. The Eagle lamp provides optimum power for the tag.
Integrated
By having the tag integrated into the cap lamp, the tag will not get left behind. This is a very important safety consideration.
Proximity tag enabled
tags developed in partnership with proximity detection solution suppliers use various cap lamp functions to alert miners of danger zones.
Programmable colored status lights
2 colored LED lights in the cap lamp can be pre-programmed by 3rd-party software (proximity-enabled model only) and are often used to differentiate proximity zones near equipment by color (e.g., yellow=caution; red=danger) or can be programmed to send messages in multiple standard sequences.
Bi-directional communication
the headpiece has 2 additional side push buttons to support bi-directional communication. The push buttons are used for a variety of functions, including, but not limited to, emergency assistance (man-down) requests, acknowledging a signal/warning or triggering a warning/alarm.
Programmable cap lamp lights
The fully programmable cap lamp status lights can be used for a variety of notifications, including safety or operational alerts, e.g., for a man-down or evacuation signal by flashing a pre-programmed sequence. It can also be used to signal shift change or report-to-surface instructions.
Flashing blue LED “Taillight”
To enhance user visibility, the taillight on the battery pack faces away from the hard hat to alert others making a rear approach.
Online/Offline indicator
Alerts user to operational status on applicable models.
Specifications
Battery Charge Time: |
< 10 hours |
Run Time: |
14 hours |
Weight: |
Single Cell: 300g (10.6oz) Double Cell: 330g (11.6oz) |
Light Output: |
Single Cell: 8500 lux Double Cell: 12500 lux |
Charger Configuration: |
Single 4, 10, 24, 48-unit |
Charger Power Source: |
120V or 240V models |
Charging Temperature: |
5°C to 35°C (optimum 15°C to 20°C) |
Operating Temperature: |
-20°C to 60°C |
Water and Dust Protection: |
IP 67 |
Resources
Data Sheet – English
Component Replacement Info
The battery and all components of the Polaris are serviceable, increasing the life of the lamp, lowering the total cost of ownership and ultimately reducing waste. Check with your authorized NLT distributor or NLT for service or training.
Warranty
SEPT 6, 2024
Northern Light Technologies (NLT) guarantees that Eclipse, Polaris and Rebel cap lamps (including Plus versions), and related charging systems, will be free of material and workmanship defects for a period of 24 months from the serialized date on the product.
Genesis, Eagle and Falcon (including plus versions) and Aries cap lamps and related charging systems and the NLT Automated Cap Lamp Output Tester will be free from defects in material and workmanship for a period of 12 months from the serialized date on the product.
For lamps with third-party electronics installed, such as tags, the warranty is based on the third-party product and excluded from this policy.
Excluded from the warranty are items or components that are prone to high wear such as: rubber components, cables, strain reliefs, covers, lenses and clips.
This warranty does not apply to NLT product performance due to the installation or integration of non-approved third-party components or solutions, such as, but not limited to tracking tags.
This warranty is conditional upon the proper use, maintenance, operation, charging, and protection according to instructions within NLT User Guides.
Northern Light Technologies’ responsibility for any loss or damages, regardless of cause, shall not exceed, under any circumstances, the original purchase price of the product to the original purchaser.
Shipping of warranty products to NLT is the responsibility of the distributor / customer. NLT will ship repaired or replaced products back at no charge.
NON-WARRANTY REPAIRS POLICY
Northern Light Technologies will repair any product that is outside the Warranty Policy under the following conditions:
- All returns must be approved by an NLT customer service representative in advance through the issuance of a Return Goods Authorization (RGA) number. Equipment returned without an RGA number will be subject to an administration surcharge of $50.00,
- Equipment returned to NLT with no fault found will be subject to a minimum troubleshooting charge of $10.00 per piece of equipment, plus shipping and handling,
Refused estimates or units that are uneconomical to repair are subject to a minimum troubleshooting charge of $10.00 per unit, - Troubleshooting charges may be applied as a discount to replacement purchases if made within 30 days,
- Shipping in both directions for non-warranty products is the responsibility of the customer,
- Repaired or replaced components are further warranted for 1 year from the repair date excluding high wear components as detailed above.
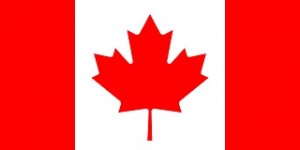
Automated Cap Lamp Output Tester
Automatic Light Beam Testing System
- Tests and logs light output in less than 10 seconds
- Easy to use
- Provides results in a Table format
- Customizable solution
- Adaptable software
- Components
- Custom-built 1.2m-long light box
- Light meter
- RFID tag reader
- Laptop/tablet running custom software (laptop/tablet supplied by the customer)
In many jurisdictions, mines are required regularly to test the light output of their lamps to ensure a minimum Lux. This manual task and corresponding documentation can be time-consuming and arduous for mine personnel. To help expedite the process, NLT has created an automated cap lamp output tester that can test and log a lamp’s light output in less than 10 seconds.
Completely customizable to work with diverse lamps/systems and logging requirements, the NLT Automated Cap Lamp Output Tester provides a seamless process that logs information and provides results in Table format which can be easily output into a report. The software has been designed so that it is simple for an administrator to set up the basic parameters and for an employee to use with little-to-no training.
Check with NLT or your authorized NLT distributor to learn more.
Note: To use system without an RFID tag, the lamp’s serial number needs to be entered each time prior to testing.
- Operator scans the part of the lamp containing the passive RFID tag.
- The first time the tag is read, the software will prompt the operator to input the unique serial number engraved on the side of the lamp. Thereafter the program will automatically recognize the lamp when the RFID tag is scanned.
- Operator turns the light to its highest setting, placing the lamp on the glass front of the light box and shining the light on the light meter located at the back of the box.
- If the light output of the lamp exceeds the easily adjustable pre-set limit set up in the software, the screen will show a green banner indicating a pass and log the lamp’s ID, Date, Time and Lux Reading.
- The program automatically resets ready for the next lamp.
SEPT 6, 2024
Northern Light Technologies (NLT) guarantees that Eclipse, Polaris and Rebel cap lamps (including Plus versions), and related charging systems, will be free of material and workmanship defects for a period of 24 months from the serialized date on the product.
Genesis, Eagle and Falcon (including plus versions) and Aries cap lamps and related charging systems and the NLT Automated Cap Lamp Output Tester will be free from defects in material and workmanship for a period of 12 months from the serialized date on the product.
For lamps with third-party electronics installed, such as tags, the warranty is based on the third-party product and excluded from this policy.
Excluded from the warranty are items or components that are prone to high wear such as: rubber components, cables, strain reliefs, covers, lenses and clips.
This warranty does not apply to NLT product performance due to the installation or integration of non-approved third-party components or solutions, such as, but not limited to tracking tags.
This warranty is conditional upon the proper use, maintenance, operation, charging, and protection according to instructions within NLT User Guides.
Northern Light Technologies’ responsibility for any loss or damages, regardless of cause, shall not exceed, under any circumstances, the original purchase price of the product to the original purchaser.
Shipping of warranty products to NLT is the responsibility of the distributor / customer. NLT will ship repaired or replaced products back at no charge.
NON-WARRANTY REPAIRS POLICY
Northern Light Technologies will repair any product that is outside the Warranty Policy under the following conditions:
- All returns must be approved by an NLT customer service representative in advance through the issuance of a Return Goods Authorization (RGA) number. Equipment returned without an RGA number will be subject to an administration surcharge of $50.00,
- Equipment returned to NLT with no fault found will be subject to a minimum troubleshooting charge of $10.00 per piece of equipment, plus shipping and handling,
Refused estimates or units that are uneconomical to repair are subject to a minimum troubleshooting charge of $10.00 per unit, - Troubleshooting charges may be applied as a discount to replacement purchases if made within 30 days,
- Shipping in both directions for non-warranty products is the responsibility of the customer,
- Repaired or replaced components are further warranted for 1 year from the repair date excluding high wear components as detailed above.